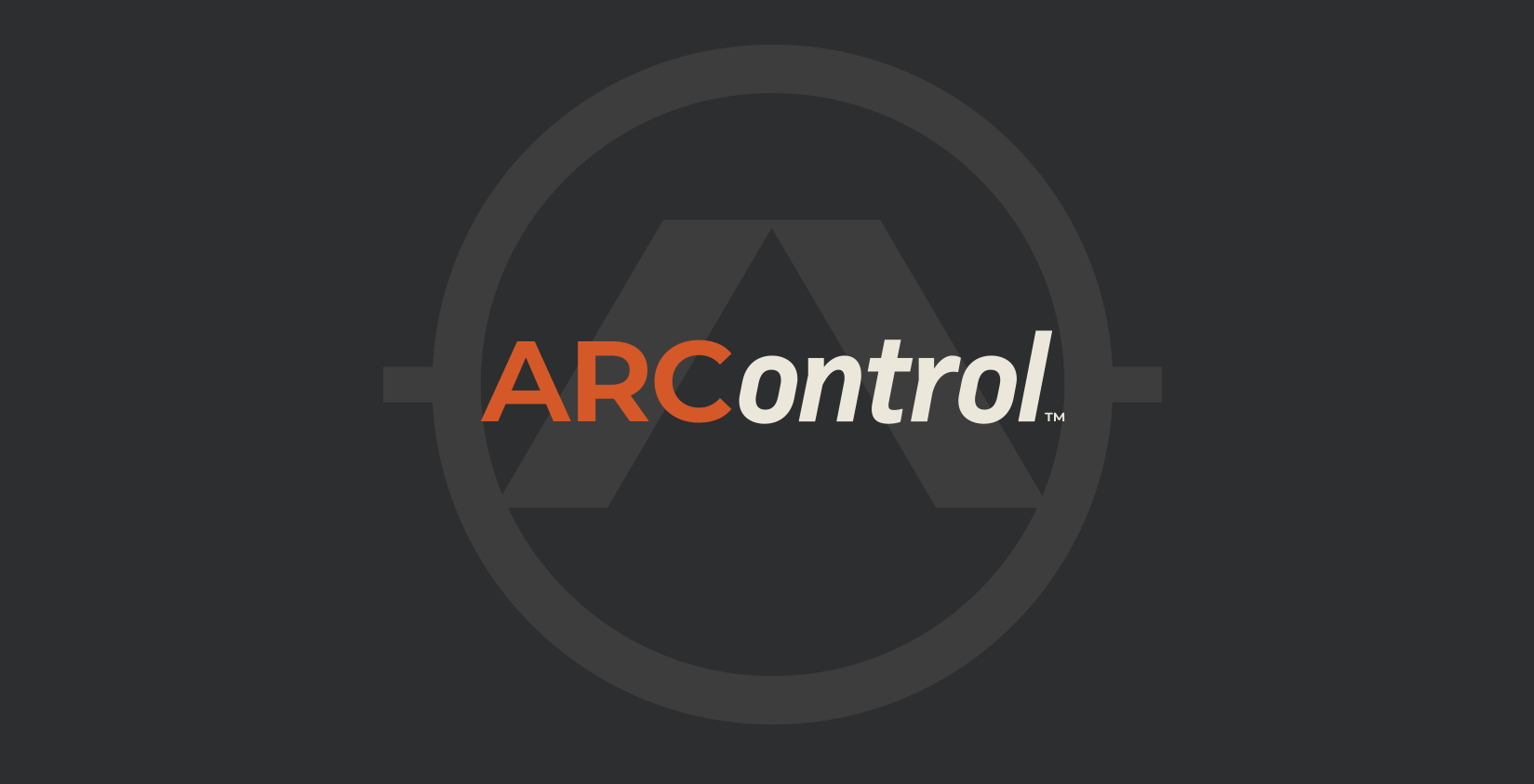
Setting the stage for the next revolution in vacuum arc remelting furnaces!
Ampere Scientific is excited to announce that its new VAR control system, “ARControl™”, is now being deployed on industrial furnaces. Trials of this revolutionary system are on the schedule for 2021. Follow us on LinkedIn to keep up to date as the results from these trials manifest!
ARControl™ is Ampere Scientific’s patented process for providing full feedback control of the arc distribution during Vacuum Arc Remelting, thus ensuring higher metal quality with higher yield margins. These outcomes are realized with ARControl™’s ability to:
Manipulate the heat flux during VAR
Characterize the arc gap between the electrode and melt pool
Disrupt unpredictable arc behavior (i.e., glows and constricted arcs)
Suppress safety critical conditions such as side arcs
Accelerate melt recipe validation
Increase yield
Increase skin quality
ARControl™ installs seamlessly on either new, or existing, VARs
A retrofitted ARControl™ installation can be completed in a few days with minimal disruption to ongoing production. With ARControl™, we give operators the ability to manipulate the arc distribution in ways not previously possible in the VAR industry.
Previously, the arc distribution could only be moderately affected using stirring coils to stabilize the arc’s random path. While their magnetic fields weakly interact with the arc, they also permeate and apply forces within the melt pool, which is not always desirable. By contrast, ARControl™ works with VARmetric™ to non-invasively measure the arc gap during the melt and apply magnetic fields to strongly interact with the arc. The controller follows up the furnace as the ingot grows, giving the melt shop direct control over the arc distribution during startup, steady-state and hot-topping.
Direct control over the arc distribution with ARControl™ give users a new tool to tailor the heat flux input to the ingot during VAR. This parameter is critical to achieve optimal quality and yield for many high value metals and is especially important for alloys which are prone to segregation defects. Furthermore, ARControl™ can monitor the melt for unpredictable arc distributions (i.e., glows and constricted arcs) that can create unwanted incursions despite operator intervention. ARControl™ gives operators the ability to disrupt these occurrences and thereby improve ingot quality.
In addition to glows and constricted arcs, side arcs are another unpredictable event during VAR. Side arcs are a safety critical condition where the arc directs its power directly to the crucible wall, potentially causing a catastrophic explosion. ARControl™ provides a new control method to suppress safety critical conditions such as side arcs. This increased safety is achieved by ARControl™’s ability to rapidly identify deleterious operating conditions and react without human intervention.
Due to the unique level of flexibility ARControl™ provides, users will have the ability to create and enhance their alloy-specific recipes. This cutting-edge technology enables individual producers to maximize both ingot yield and furnace electrical efficiency. These increased capabilities not only result in faster recipe generation and validation, but also can accelerate profitability while creating and maintaining a durable record of melt conditions. These records will include defect prediction and avoidance. In addition, ARControl™ allows companies to realize increased quality through tighter controls over melting parameters. These parameters will include arc location, arc gap, and drip short optimization, as our continued development of the ARControl™ system is leading towards a precise measurement of the arc gap length across the electrode tip. Our patented technology offers such fine control that its utilization with your furnace will result in an increased yield by ‘quieting’ the arc dynamics, causing less shelf formation, therefore reducing the potential of fall-in and improving sidewall quality.